What Is Linear Filling Machine?
A linear filling machine is a type of packaging machine that is used to fill containers, such as bottles or bags, with a specific volume of liquid or other product. These machines are designed to fill containers in a linear or straight line, moving them along a conveyor belt or other system to ensure that each container is filled accurately and efficiently. Linear fillers can be used in a variety of industries, including food and beverage, pharmaceuticals, and consumer products. They are often used in high-volume production environments, where they can help to increase productivity and reduce labor costs.
Which Industries Use Linear Filling Machine?
Linear filling machines are used in a variety of industries, including food and beverage, pharmaceuticals, and consumer products. These machines are often used in high-volume production environments, where they can help to increase productivity and reduce labor costs. In the food and beverage industry, for example, linear fillers are commonly used to fill bottles with beverages such as water, soda, and juice. In the pharmaceutical industry, they may be used to fill containers with medication, vitamins, and other health products. And in the consumer products industry, they may be used to fill containers with products such as detergents, cleaning solutions, and personal care items.
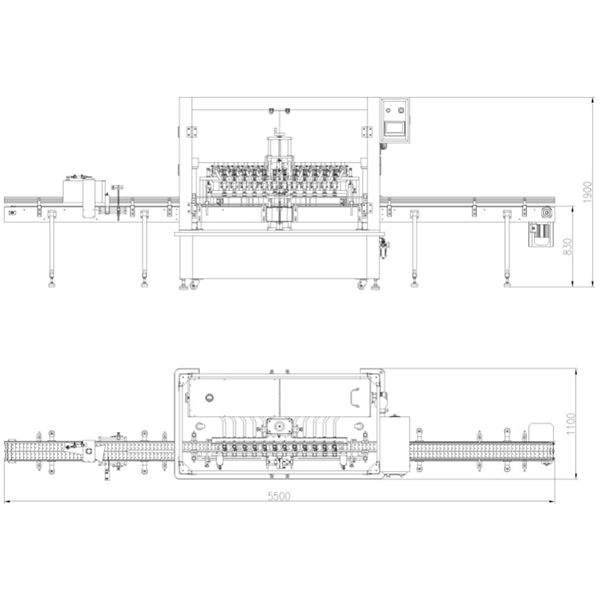
How The Linear Filler Works?
Linear filling machines typically operate by using a conveyor belt or other system to move containers through the filling process. The containers are first loaded onto the conveyor belt, and then they are moved along the belt to the filling station. At the filling station, the machine uses a variety of techniques to dispense the product into the container, such as gravity filling, pressure filling, or volumetric filling. Once the container is filled, it is sealed and moved along the conveyor belt to the next step in the packaging process. Linear fillers are typically highly automated, with sensors and other controls to ensure that each container is filled accurately and consistently.
What Are The Advantages Of Using A Linear Filling Machine?
There are several advantages to using a linear filling machine, including the following:
- Increased productivity: Linear fillers are designed to fill containers quickly and efficiently, allowing manufacturers to increase their production rates and output.
- Improved accuracy: Linear fillers are highly accurate, using sensors and other controls to ensure that each container is filled to the correct volume. This helps to prevent waste and improve product quality.
- Reduced labor costs: Linear filling machines are highly automated, requiring minimal operator intervention. This can help to reduce labor costs and improve the overall efficiency of the packaging process.
- Enhanced safety: Linear fillers are designed to be safe and easy to operate, with built-in safety features to protect operators and prevent accidents.
- Flexibility: Linear fillers can be easily customized to handle a wide range of container sizes and filling volumes, making them versatile and adaptable to different production needs.
What Are The Main Parts Of Linear Filling Machine?
The main parts of a linear filling machine include the following:
Conveyor belt: The conveyor belt is the main component of the linear filler, and is used to move containers through the filling process. It may be made of a variety of materials, such as plastic, rubber, or metal, depending on the specific requirements of the application.
Filling station: The filling station is the part of the machine where the product is dispensed into the container. It may use gravity filling, pressure filling, or volumetric filling, depending on the type of product and the required filling volume.
Control panel: The control panel is where the operator can set the filling parameters and monitor the operation of the linear filling machine. It may include buttons, dials, and displays to control and adjust the filling process.
Sensors: Sensors are used to monitor the filling process and ensure that each container is filled accurately and consistently. They may include level sensors, flow sensors, and weight sensors, depending on the specific requirements of the application.
Sealing station: The sealing station is where the container is sealed after it has been filled. This may be done using heat sealing, adhesive sealing, or other methods, depending on the type of container and the product being packaged.
What Are The Functions Of The Linear Filling Machine?
The main functions of a linear filling machine are to fill containers with a specific volume of product, seal the containers, and move them along a conveyor belt or other system for further processing or packaging. Linear fillers typically use a variety of techniques to dispense the product into the container, such as gravity filling, pressure filling, or volumetric filling. They are also equipped with sensors and other controls to ensure that each container is filled accurately and consistently. In addition, linear fillers may include other functions, such as labeling, capping, and coding, to further enhance the packaging process.
What Are The Types Of Linear Filling Machines?
There are several types of linear fillers, including the following:
Gravity filling machine: A gravity filling machine uses the force of gravity to dispense the product into the container. It is typically used for products with a low viscosity, such as water, juice, and other beverages.
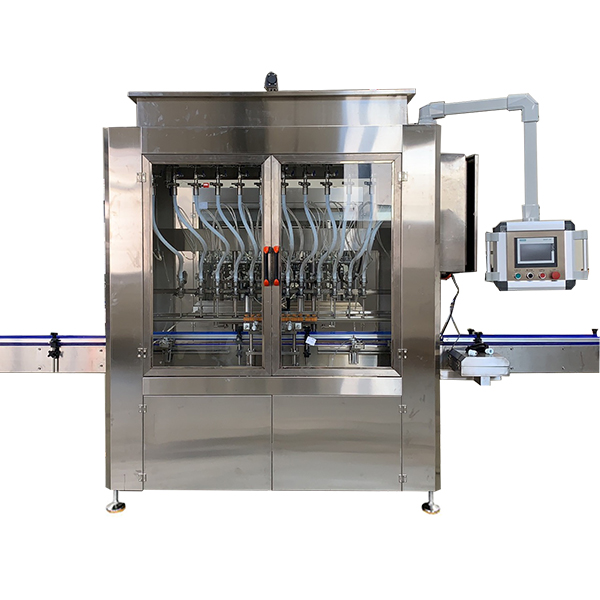
Volumetric filling machine: A volumetric filling machine dispenses the product using a specific volume or weight measurement. It is often used for products that require precise filling, such as medications and other pharmaceutical products.
Time-gravity filling machine: A time-gravity filling machine combines the principles of gravity filling and volumetric filling. It uses a timing mechanism to control the flow of the product, allowing it to be dispensed at a specific rate and volume.
Pump filling machine: A pump filling machine uses a piston or other mechanical pump to dispense the product into the container. It is often used for products that are difficult to fill using gravity or pressure, such as thick or viscous liquids, or products with particulates.
How To Choose Linear Filling Machine?
When choosing a linear filler, there are several factors to consider, including the following:
Type of product: The type of product to be filled will determine the type of linear filler that is most suitable. For example, products with a low viscosity, such as water, juice, and other beverages, can be filled using a gravity filling machine, while products with a higher viscosity, such as sauces, syrups, and other thick liquids, may require a pressure filling machine.
Filling volume: The required filling volume will also affect the type of linear filler that is best suited for the application. For products that require precise filling, such as medications and other pharmaceutical products, a volumetric filling machine may be the best choice.
Container type: The type of container to be filled will also impact the selection of a linear filling machine. Different machines are designed to handle different types of containers, such as bottles, bags, pouches, or cans, so it is important to choose a machine that is compatible with the containers being used.
Production rate: The production rate, or the number of containers to be filled per hour, will also influence the selection of a linear filling machine. Higher-speed machines can fill more containers per hour, but they may also be more expensive and require more space and power.
Budget: The budget for the linear filler is also an important factor to consider. Different machines have different price points, and it is important to choose a machine that fits within the available budget while also meeting the other requirements of the application.
Linear Filling Machine Vs Rotary Filling Machine
The main difference between a linear filler and a rotary filling machine is the way in which the containers are moved through the filling process. A linear filler uses a conveyor belt or other system to move the containers in a straight line, while a rotary filling machine uses a rotating platform to move the containers in a circular pattern. This difference in motion affects the overall design and operation of the filling machine. Linear filling machines are typically more compact and can be easily integrated into a production line, while rotary filling machines are larger and more complex, but can handle a higher volume of containers.
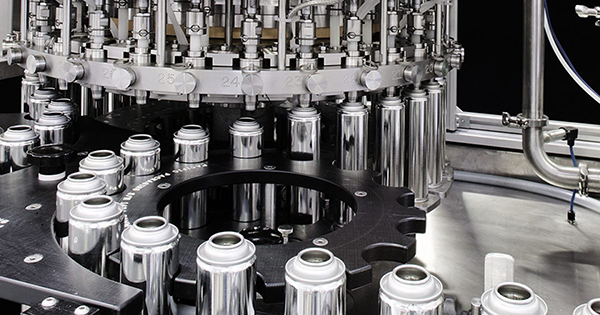
How Many Bottles Can A Linear Filling Machine Fill Per Minute?
The number of bottles that a linear filler can fill per minute will depend on a variety of factors, including the speed of the conveyor belt, the size of the bottles, and the type of filling process being used. Linear fillers are designed to fill containers quickly and efficiently, and can typically fill several hundred bottles per minute. However, the exact number will vary depending on the specific characteristics of the machine and the application. It is important to consult the manufacturer's specifications to determine the exact filling capacity of a particular linear filling machine.
Which Containers Can Be Filled By The Filler?
Linear fillers are designed to fill a wide range of containers, including bottles, bags, pouches, and cans. The specific types of containers that can be filled will depend on the design of the filling machine and the type of product being packaged. Some linear fillers are versatile and can handle a variety of container shapes and sizes, while others are designed to fill specific types of containers. It is important to consult the manufacturer's specifications to determine the types of containers that can be filled by a particular linear filling machine.
How To Clean The Linear Filling Machine?
Cleaning a linear filler is an important part of maintaining its performance and ensuring the quality of the products being packaged. The specific cleaning steps will depend on the design of the machine and the type of product being packaged. In general, however, the following steps can be used to clean a linear filling machine:
- Disconnect the machine from any power sources and remove any containers or packaging materials from the machine.
- Using a soft cloth or brush, clean any visible dirt or debris from the machine, including the conveyor belt, filling station, and control panel.
- Depending on the type of product being packaged, it may be necessary to disassemble certain parts of the machine for cleaning, such as the filling nozzles or sealing stations. Refer to the manufacturer's instructions for specific disassembly and cleaning instructions.
- Once all visible dirt and debris have been removed, use a cleaning solution appropriate for the type of product being packaged to clean the machine. This may be a mild detergent, a sanitizing solution, or another type of cleaner, depending on the specific requirements of the application.
- Use a soft cloth or sponge to apply the cleaning solution to the machine, making sure to cover all surfaces and areas that come into contact with the product.
- Allow the cleaning solution to soak for the recommended amount of time, then use a clean cloth or sponge to remove the solution and any remaining dirt or debris from the machine.
- Rinse the machine with clean water, making sure to remove any remaining cleaning solution and debris.
- Once the machine is clean and dry, reassemble any parts that were disassembled for cleaning, and reconnect the machine to any power sources.
It is important to follow the manufacturer's instructions for cleaning the linear filling machine to ensure that it is done properly and that the machine is not damaged. Regular cleaning is also important to prevent contamination and ensure the quality of the products being packaged.
VKPAK offers many types of linear fillers, if you are looking for a linear filler, please contact us.